Baltic Robot Battle Competition – victory of the Melsoniaki team
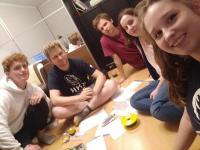
Melsoniaki Team while brainstorming, photo by: Robotics Student Research Group (KNR)
The students of the Robotics Student Research Group (at the Faculty of Power and Aeronautical Engineering) won two first prizes in the Baltic Robot Battle Competition 2020. The Melsoniaki Team, composed of students who designed the humanoid robot Melson, won the RoboHackathon with their BoBeR robot, while Wisienka, a robot designed by Kornelia Łukojć, was awarded the title of Miss BBR.
The Baltic Robot Battle Competition, organised by the Robotics Association SKALP based in Gdańsk, was held from 25 to 27 September. Due to the pandemic, this year’s Competition was held online.
The members of the Melsoniaki Team are: Bartosz Bok, Dominik Górczyński, Kornelia Łukojć, Kacper Mikołajczyk, Konrad Szczerbiak and Larysa Zaremba.
What happened during the competition? We give the floor to our team.
FRIDAY, 25 SEPTEMBER
Breeding ground for ideas
The Competition started on Friday, September 25, at 07.00 pm. Precisely at that time the competition task was published and the RoboHackaton was “on”. The teams were given the task to make a robot which would in an autonomous way draw “BBR 2020”. The organisers left us freedom to be creative – no additional requirements were specified as to the robot or the manner of drawing the caption.
We immediately started brainstorming and came up with the key elements – the decision to make a Cartesian robot and to have the caption written with the use of long-exposure photography. We settled the details by discussing all the possible difficulties that the construction works could have posed. We also rejected other ideas, including drawing the caption with a parallel robot on the wall, drawing on two tracks or displaying “2020” in a binary form.
Melsoniaki Team while brainstorming, photo by: Robotics Student Research Group (KNR)
The main idea was then clear – we would draw the caption with the use of LED diodes and a Cartesian robot. The robot was planned to have four engines with wheels moving the robot back and forward. The device was designed to have nearly 1.5 m in width, and its arm was planned to be made of 3D printed elements, joined with long PVC tubes as a support for a small trolley moving to the left and to the right with the use of another two engines. The trolley was designed to be moving on 4 drive wheels and 2 idler pulleys, to ensure a steady movement without the risk of falling off the tracks.
With such support, the trolley with the diodes would be able to move along two axes.
Promising test results
In order to give the robot information on the position of the trolley in real time, we decided to use mechanical encoders, providing information on the angular position of the robot’s wheels, and also an optical encoder we had constructed, which provided information on the position of the trolley. To this purpose we decided to place a batten between the two PVC tubes, covered with alternating white and black stripes. In this way, the digital sensor placed underneath the trolley would signal whether at the particular moment it was over the black or white surface. By counting the subsequent stripes, we would be able to establish the location of the trolley with accuracy of 1.5 cm.
At first, we thought to use the Arduino platform, however, we quickly rejected this idea as it did not have a sufficient number of proper peripheries. In the end we settled for NucleoSTM32F1 platform, with which we could control 6 engines, light up the LED diodes and read the data from the encoders.
It was almost 11 pm, so we settled the most important construction issues. What was left was to perform a test to check if we could take a good photo with the caption. The test went well. We gathered all the necessary elements that we had on us: engines, wheels, H-bridges controlling the engines, LED diodes, mechanical encoders, the optical sensor and the wires. We also made a list of those elements that had to be bought first thing Saturday morning. The next step was the beginning of the construction process.
SATURDAY, 26 SEPTEMBER
First – the trolley
Next morning some of us went to buy the PVC tubes, the batten for the encoder, screws and nuts. The 3D printers were working all night and around 10am the key components of the trolley were ready. The work on the code for the robot was also under way. At first, we tested programs for different sensors separately. Then, we moved to the NucleoSTM32F3 platform where we had the optical sensors and mechanical sensors operating already before noon.
In order to create the robot, we chose STM32CubeMX and the main code was written in the C programming language with the use of Atollic TrueStudio and diagnosed with STM32Studio, among other things. Then, our programmers and electronics engineers started working on the H-bridges to control the engines. Everyone worked hard and soon the engine made its first spin.
In the meantime, we had designed the track of the trolley and started to write the code for steering with the use of the state machine. We resolved to simplify the “BBR” caption so that is included only straight lines.
Before the final construction was ready, the code was written based on the prototype electronics, photo by: Robotics Student Research Group (KNR)
Work in progress
While some of us worked on the code, others took care of the necessary soldering, drilling and 3D printing. In the afternoon we were able to admire the trolley moving along the mounted PVC tubes and the code for all electronic parts, including the Bluetooth module which was to help in subsequent code testing and with insight into the variables in real time or with the start of the robot movement.
At that time, we communicated with the organizers. We also decided it was time for a short break and a meal.
A problem? A problem solved!
In the afternoon the mechanical construction was growing fast, and all the time new electronic and mechanical elements were added. Also, the first functions necessary to control the robot were ready in the code. In the evening all parts were already where they were supposed to be according to the design.
We encountered also the first problems, such as too high power consumption of the six LED diodes placed on the trolley and used for drawing. However, the matter was quickly resolved with a new circuit board and diagram.
SUNDAY 27 SEPTEMBER
What do rain and robots have in common?
Our main idea that we came up with on Friday was to draw the largest possible caption with diodes and long-exposure photography. Already during our first conversation with the organizers, they indicated a small albeit important detail – the weather forecast for the night from Saturday to Sunday. We had planned to take the photo outside and during the night but that proved to be impossible due to heavy rain.
It became clear we had to take the photo in the apartment where we had constructed the robot. This heavily complicated our task. At that stage we were not able to take the photo from above the robot. We were also limited by the space in which it could move.
We were quick to stop worrying about this though – our robot started to move around!
First drive of the trolley, photo by: Robotics Student Research Group (KNR)
Too long a caption
Of course, at first it drove in the wrong direction and with insufficient speed, but after a while our module-controlled trolley was driving left and right, back and forward, while the impulses from the encoders fed the variables.
That is when we started intensive tests of the robot’s motion path. It soon became obvious that drawing the entire “BBR 2020” caption would be too difficult as it was simply too long compared to the surface we had at our disposal.
We made a strategic decision to write too captions – “BBR” and “2020”.
Two-hour nap
After some long tests the “BBR” caption was ready. All that was left to do was to take the photo. Around 5.38 am the processing of the photo ended and those of us who were not asleep at that time could admire the final photo of the “BBR” caption.
At 5.45 am we decided that we all needed some rest and we would go to sleep for the subsequent two hours.
At 08.05 am sharp we were up and working.
The “BBR” caption, photo by: Robotics Student Research Group (KNR)
Reconnecting needed!
Then, we had to deal with “2020”. We were in a hurry because the end of the hackathon was planned for 12am.
At the same time, we started working on the final video of the Melsoniaki team and a name for our robot – we chose to name it “BoBeR”, a robot able to “capture what is fleeting”.
The robot was already smoothly writing “20”. And this is when a critical failure occurred – when loading the full “2020” caption the connection between the Nucleo platform and the computer broke down. It was already 10.00 am and we had to reconnect all the cables from one platform to another, identical one.
However, we still experienced problems with the connection between the board and all elements, so we decided to finish the second part of the caption in another manner. We chose to drive the trolley the entire length of the robot and display the caption by switching on/off the diodes in a sequence of “11111100100”. The task went well. It was not even noon yet when we delivered our results to the organizers.
The “2020” written in a binary form, photo by: Robotics Student Research Group (KNR)
Outburst of creativity
At 2.00pm the videos with the projects from all teams were published.
Other teams managed to handle the task in an equally creative manner. The „Ten łazik nigdzie nie poleci” team wrote the caption with whipped cream (“BBR 202”) and glowing cucumbers (“0”), while the teams named “Najgorszy rocznik w historii szkoły” and “Dajemy miodu” decided to make the caption with the use of a mobile robot equipped with a marker.
The winning robots
At 4.00pm the results of all competitions of the Baltic Robot Battle were announced. To our great joy, the robot named Wisienka constructed by Kornelia Łukojć won the Miss BBR 2020 title. The task here was to submit a description of the robot, its application and achievements. The organizers acknowledged the advanced construction of the robot and how it was made. (Last year the robot won the second prize in the MiniSumo competition during the Baltic Robot Battle Competition 2019).
Then, the moment we had been all waiting for arrived – the announcement of the RoboHackathon results.
Our BoBeR won so we were over the moon.
We spent those days and nights working hard and our effort was recognized. Our cooperation was very smooth and everyone contributed to the project with their best ideas and skills.
We are happy that the robot turned out to be up to the task although some problems appeared along the way, but this is typical for this type of competition.
You may see the results of our work in the photos and the video.
The video coverage of the competition is available on the YouTube channel of the Robotics Association SKALP. It includes our conversations with the organizers and numerous lectures.
The moment when Wisienka won the Miss BBR 2020 title, photo by: Robotics Student Research Group (KNR)
The BoBer Robot, photo by: Robotics Student Research Group (KNR)
The size of the BoBeR robot as compared to a person, photo by: Robotics Student Research Group (KNR)