Innovative materials for the manufacture of prosthetic limbs
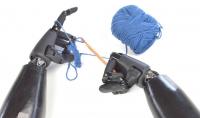
Teams from the Faculty of Chemistry, Faculty of Materials Science and Engineering and Faculty of Power and Aeronautical Engineering are involved in the research, photo Pixabay
Even up to 60 million people worldwide do not have a fragment of a limb, and are in need of prosthesis. But this is a truly complex process, requiring a lot of time and money. Researchers from several teams of the Warsaw University of Technology have joined forces to find an alternative to the solutions currently applied. Joanna Ryszkowska, from the WUT Faculty of Materials Science and Engineering, is talking about the results of their work and plans for the future.
Materials are crucial
Cosmetic, mechanical and bionic prostheses – may differ in appearance, complexity and functionality. Still, they are all supposed to help in everyday life. For this to be the case, they must be made of appropriate materials.
– These materials, depending on where the prostheses will be implemented, should have different mechanical characteristics, and also fulfil various functions, e.g. good transmission of high stresses or vibrations (...), serve to mount (...) the structure, protect electronics (...) – explains Prof. Ryszkowska.
Researchers from the WUT focused in their project on materials for cosmetic prostheses. Although such a prosthesis is not incredibly technologically advanced, it still contains details that need to be borne in mind and taken care of.
Almost like an astronaut
To mount a prosthesis on a stump, you need a so-called prosthetic socket. It is usually made of silicone rubber, which results in a number of problems. First of all, the material makes the stump sweat. Secondly, it is difficult to transfer tension from the stump to the prosthesis.
However, the element connecting the socket with the stump may be an insert, of course, made of a well-chosen material.
'We have proposed a transitional material to absorb sweat,' says Prof. Ryszkowska. – After removing (...) the prosthesis, such material can be washed (...) and will still be functional.
This material is open-cell polyurethane foams. Such foams are used, for example, to protect astronauts as they fly into space.
Challenge after Challenge
The insert between the stump and the prosthetic socket is one thing. But the socket itself must also be properly made – so that it combines durability with flexibility.
– In the first prototypes (...) of cosmetic prostheses, the socket was made of thermoplastic polyurethane – says Prof. Ryszkowska. – (...) For now, we have a small range (...) of polyurethane elastomers that can be used (...), the first ones were too rigid.
The level of challenge is constantly growing, because the next element of the prosthesis are the joints – very complicated constructions, because they are associated with joints, and therefore movable. Polyamides are used to make them.
– We modify polyamides in terms of changing functional features (...), in order for them not to clash, so that the mechanism can work reliably as long as possible (...) – Prof. Ryszkowska explains. We are developing new composites that will be able to work in these demanding applications in prosthesis joints. We want these composites also to be produced using 3D printing techniques, so that it [is] easier and faster (...). There are a lot of materials that we want to check and verify as part of the project.
The last stage of the work will be the production of the first prosthesis, which will allow to verify the suitability of the materials used. Of course, that will take time.
Interfaculty cooperation
The project "Polymeric materials with diverse mechanical and functional characteristics, intended for the production of limb prostheses using additive techniques" is financed under the program "Excellence Initiative – Research University" implemented at the Warsaw University of Technology. The idea received support in the competition Technologies-Material-2: Advanced.
Several teams from the WUT are involved in the research: from the Faculty of Chemistry (responsible for the modification of polyamides for moving elements of prostheses), the Faculty of Materials Science and Engineering (dealing with foams and polyurethane elastomers), the Faculty of Power and Aeronautical Engineering (specializing in 3D printing). Maciej Dębowski, PhD, from the Faculty of Chemistry is the head of the entire project.